Shock Tube Research Facility
Overview
The Virginia Tech Shock Tube Research Facility is a unique academic resource equipped with a large-scale gas-detonation blast simulator and state-of-the-art high-speed data acquisition and camera systems. The blast simulator is designed to produce high pressure blast waves that accurately simulate those generated by accidental explosions and terrorist bombings. It is used to evaluate the resilience of structural and non-structural building components subjected to extreme blast loads, including loadbearing elements, walls, windows, and exterior cladding. Other applications include fundamental study of material behavior under high strain rate loading and development and validation of new structural systems for enhanced energy dissipation.
Types of Tests Supported
Planar and non-planar test specimens up to 10 ft x 10 ft (3.0 m x 3.0 m) square may be mounted to the reaction frame for simulated blast testing. Large planar targets may be mounted directly to the reaction frame. Planar targets that do not cover the entire blast flow area (e.g., windows, doors) are installed in a target holder that is mounted to the reaction frame. For the case of non-planar targets (e.g., beams, columns, connections, etc.), a load transfer device is used to collect and apply blast pressures to the target as a series of inertial point loads.
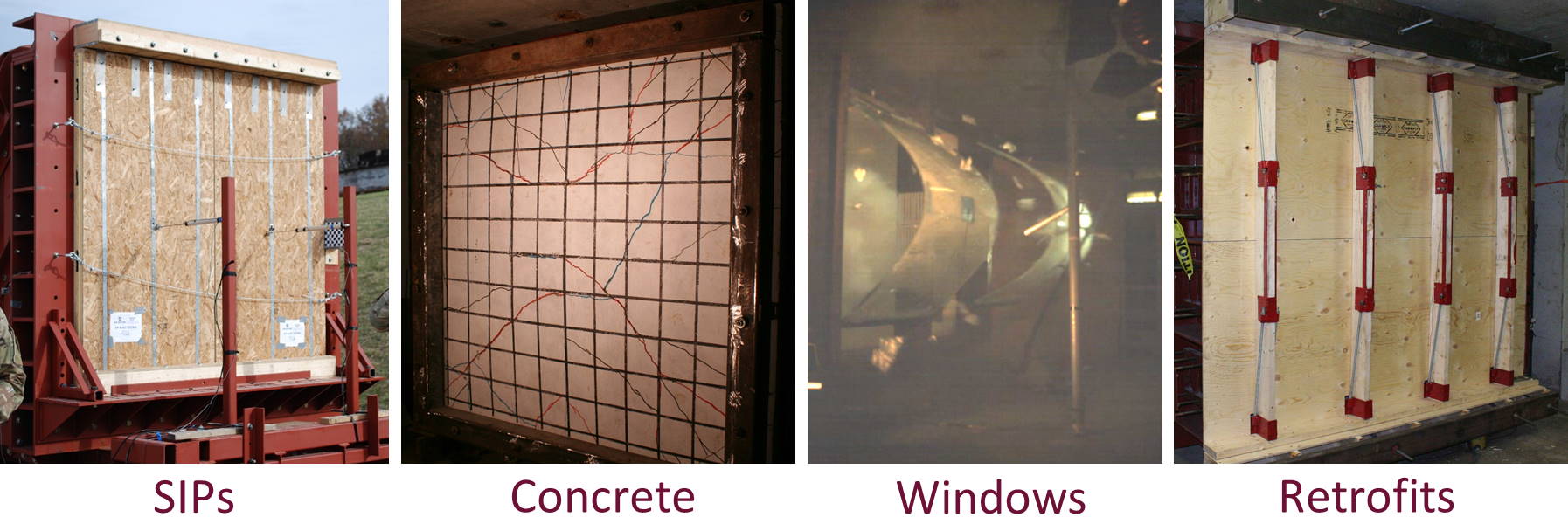
Operating Characteristics
The Virginia Tech Shock Tube generates high pressure, short-duration shock waves similar to those produced by the detonation of high explosives. The shock waves produced by the blast simulator are characterized by a near instaneous rise to peak pressure followed by an exponential decay over the positive phase. After this period, the pressure will drop to ambient atmospheric conditions. Secondary and teriary reflections, a by-product of shock wave propegation in the tube, are controlled through the use of louvres. The gas-detonation driven shock tube has been demonstrated to produce planar shock waves and generate repeatable pressure-impulse combinations at the location of the test frame.
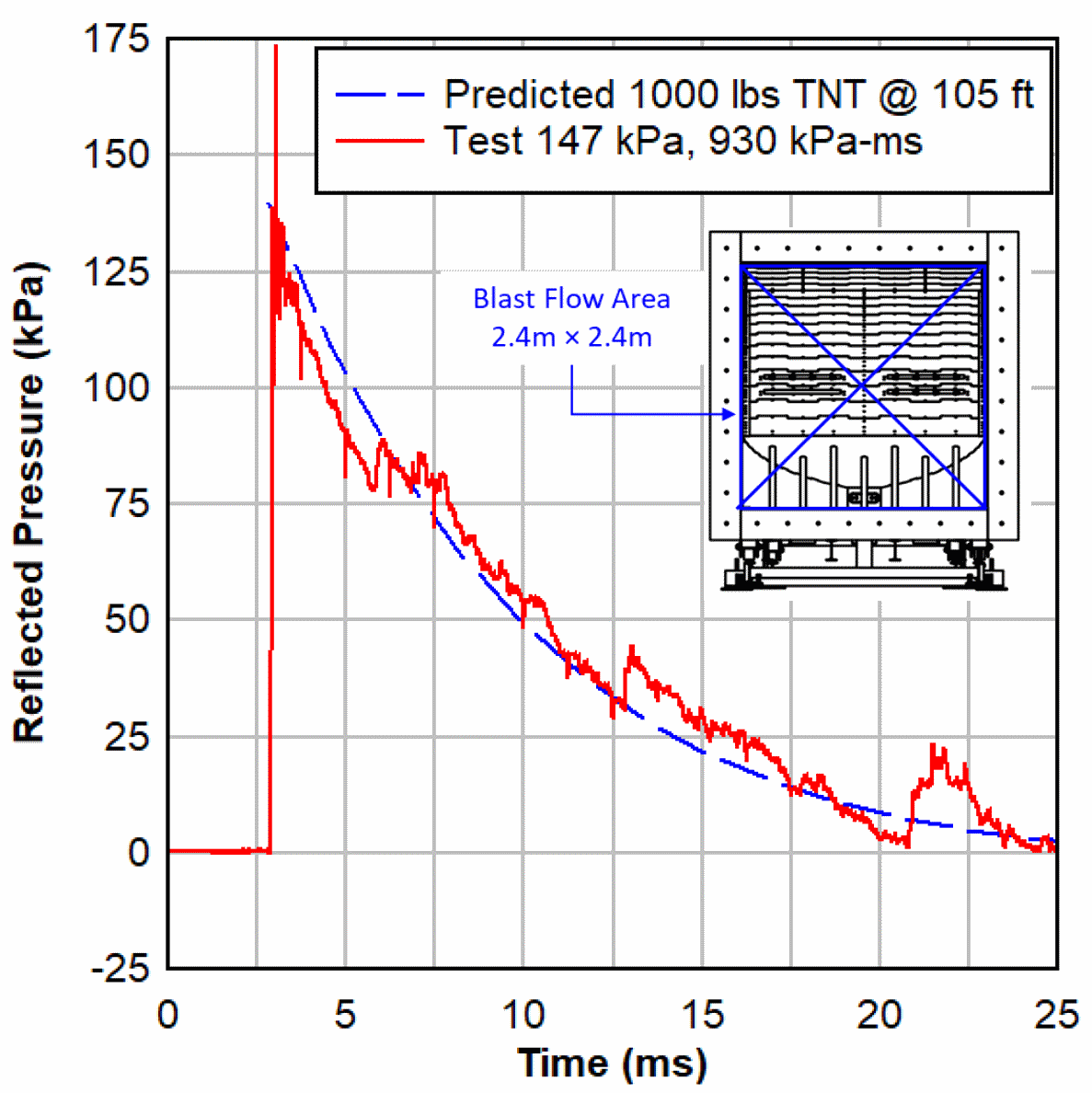
The shock tube is driven by the detonation of a reactive gas mixture. In most cases, a stoichiometric mixture of oxygen and acetylene is used, expressed by the following reaction: $$2C_{2}H_{2}+5O_{2}\rightarrow 4CO_{2}+2H_{2}O+\Delta E $$ The driver portion of the shock tube, known as the detonation chamber, is filled with gas contained by a thin barrier material. A small pyrotechnic charge is used to ignite the mixture. One of the key advantages of detonation driven shock tubes is that thin barrier materials used as diaphragms do not impede shock wave propagation as long as there is no differential pressure between the driver and driven sections before ignition. Detonation driven shock tubes also generate more realistic blast profiles than comparable compressed-gas shock tubes since expansion of compressed gas out of the driver creates a “jet effect” that alters the impulse imparted to the target.
The operating range of the shock tube is defined in terms of peak reflected pressure, reflected impulse, and positive phase duration. The operating characteristics are controlled by selecting an appropriate oxy-fuel gas mixture and volume to achieve desired blast parameters. The figure below shows a scatter plot of maximum recorded reflected pressures versus reflected impulse for different oxy-acetylene driver gas volumes. A high degree of control in blast wave characteristics is achieved using the oxy-fuel driver system. For reference purposes, the practical upper limit on shock tube capacity, 30 psi (200 kPa) and 290 psi-ms (2000 kPa-ms), represents an equivalent hemispherical detonation of 6100 lbs (2800 kg) of TNT at 170 ft (51 m), corresponding to a scaled distance $Z=9.2 ft/lb^{1/3}, (3.6 m/kg^{1/3}$).
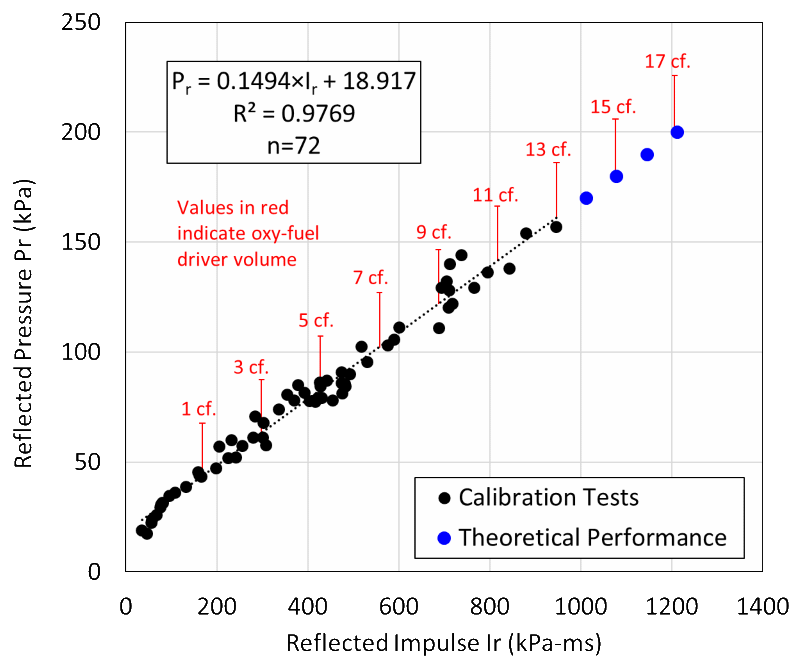
Specifications
The construciton and performance specifications of the blast simulator are as follows:
- 30 psi (200 kPa) applied reflected pressure
- 5-20+ millisecond positive phase duration
- Far-field explosive pressure waveform
- Oxy-fuel gas-detonation drive
- Versatile specimen mounting frame, 10 ft x 10 ft (3.0 m x 3.0 m)
- Blast pressure flow area, 8 ft x 8 ft (2.4 m x 2.4 m)
- Footprint: 67 ft x 12 ft x 14 ft (20 m x 3.6 m x 4.2 m)
- Mass: 75,000+ lbs (34,000+ kg)
- Remote filling, firing, and operating station
- Computer controlled gas filling & metering
Instrumentation
A eighteen-channel high-speed digital data acquisition system recording at 800,000 samples per second per channel is available to measure the blast pressure profile and monitor the displacements, strains, reactions and accelerations of the test specimens. The system is triggered when one of the pressure sensors records a pressure in excess of a predetermined threshold. High-speed HD video cameras capturing 2,000 frames per second are employed to record the response of the test specimens from various vantage points, depending on the research needs of the project. A wide array of contact and non-contact displacement transducers, piezoresistive pressure gauges, accelerometers, load cells, and other instruments are available for measurement sensing.
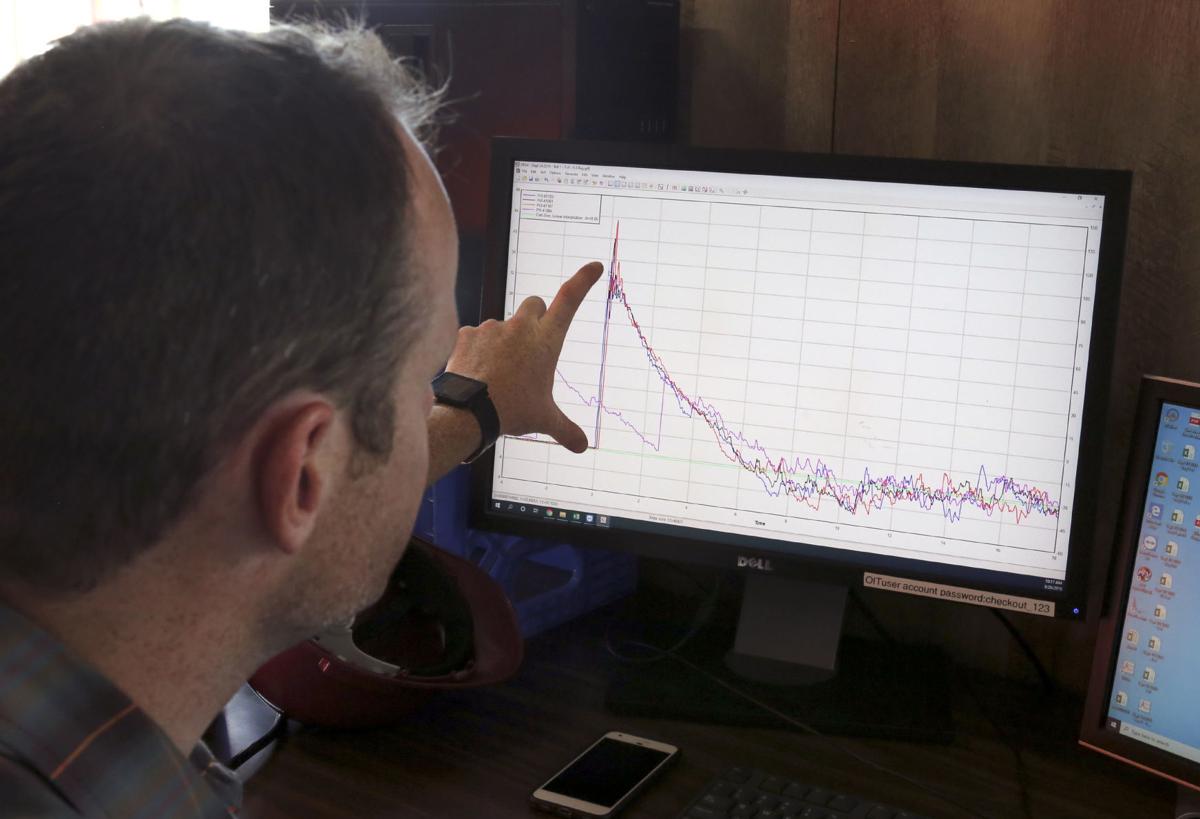